Which 3D Printing Techniques Create Strong, Functional Parts?
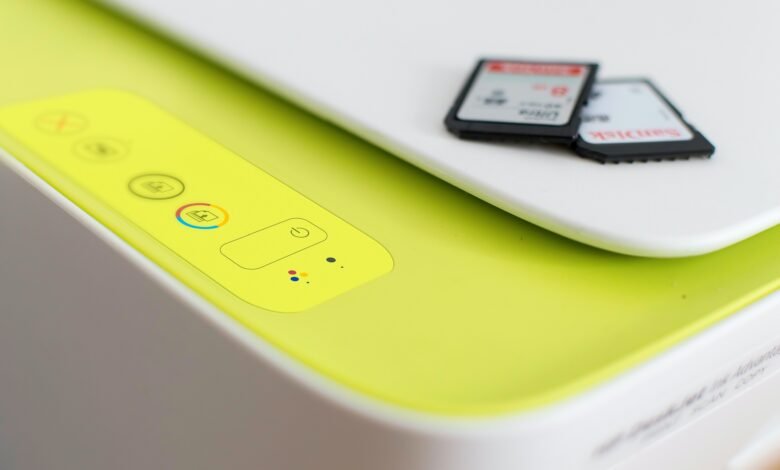
In the realm of 3D printing, there’s an expansive 3D model library that artists and engineers can tap into. However, the strength and functionality of the final product hinge significantly on the chosen 3D printing technique.
Some methods offer a clear edge when the primary objective is to create parts that are not only aesthetically pleasing but also robust and functional. Here’s a deeper dive into five such techniques. Adobe says, “Create and visualize products with unlimited variations.”
Fused Deposition Modeling (FDM): A Versatile Choice
Fused Deposition Modeling, commonly known as FDM, is one of the most popular 3D printing techniques. It works by melting a thermoplastic filament and depositing it layer by layer to create a 3D object.
This method is widely celebrated for its versatility, supporting a range of materials, including ABS, PLA, and nylon, among others. Consequently, FDM can produce parts with varying degrees of strength, flexibility, and resistance to heat and chemicals, making it a prime choice for functional parts.
Moreover, FDM 3D printers come in a wide range of sizes and prices, making them accessible to hobbyists, professionals, and industries alike. With the availability of composite filaments, such as carbon fiber-infused PLA or nylon, FDM can further enhance the strength and mechanical properties of the printed parts.
Stereolithography (SLA): Precision Meets Strength
Stereolithography, or SLA, is another 3D printing technique that excels in creating strong, functional parts. It uses a laser to cure a photosensitive resin, layer by layer, to form the final object. The standout characteristic of SLA is its high resolution and precision, which result in smooth surface finishes and intricate details.
While SLA parts might not be as robust as those made by FDM, they offer superior tensile strength and can withstand high stress when flexed, which is beneficial for certain applications.
Selective Laser Sintering (SLS): For Complex Geometries
Selective Laser Sintering, abbreviated as SLS, uses a high-power laser to fuse tiny particles of plastic, metal, ceramic, or glass powders into a 3D object. Unlike FDM and SLA, which require support structures for overhanging parts, SLS allows the creation of complex geometries without any support.
This gives it a distinct advantage in creating robust, functional parts with intricate designs. Moreover, parts made with SLS are generally strong, resistant to heat, and durable, opening up a world of potential applications.
Direct Metal Laser Sintering (DMLS): A Metal Marvel
For applications requiring metal parts, Direct Metal Laser Sintering (DMLS) emerges as a reliable choice. DMLS is a powder bed fusion technique similar to SLS but works with metal powders. This process allows for the creation of metal parts that are incredibly strong and capable of withstanding high temperatures and pressures. While the cost and complexity of DMLS are higher than other techniques, its ability to produce high-strength, functional metal parts makes it a go-to choice for industries like aerospace and automotive.
Multi Jet Fusion (MJF): Fast and Functional
Multi Jet Fusion, or MJF, is a relatively new 3D printing technique developed by HP. It utilizes a fine powder and fuses it using inkjet technology to create the 3D object. MJF can produce parts faster than many other techniques without compromising strength or detail. This process results in parts that are dense, uniform, and strong, making it an excellent choice for functional applications.
The choice of 3D printing technique is pivotal when strength and functionality are priorities. While FDM offers versatility, SLA shines in precision, SLS excels in complexity, DMLS delivers in metal applications, and MJF stands out in speed. By understanding the advantages of each technique, designers and engineers can better utilize their 3D model library to produce parts that truly bring their designs to life.